







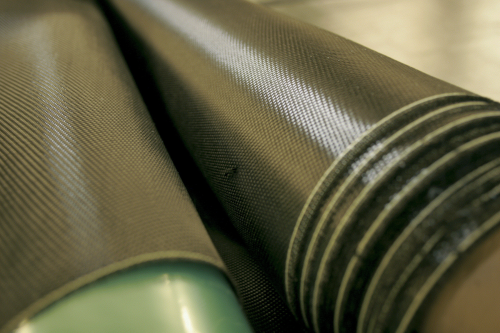

Roy Heiner (technical director of the ABN AMRO syndicate) chose Juan Kouyoumdjian as designer, hired Killian Bushe (supervisor boat building) and had the boats built at the well facilitated yard of Leen Schaap in Lelystad, Holland (Schaap Shipcare).
Currently living in Sweden, Irishmen Bushe also built the winning VO60 in the the 2001-2002 Volvo Ocean Race: Illbruck. Right now Bushe is doing some modifications on the Americas Cup Boats for Victory Challenge in Gothenburg. So Bushe is not unknown in the boat building world. But there was a lot of buzz about the choice of the relatively unknown Argentinian Kouyoumd-jian, who lives in Spain. The last five winning Whitbread/Volvo boats were all designed by Bruce Farr. Four of the seven boats which are competing in the present edition are therefore designed by Farr.
Heiner explains why he chose for Kouyoumdjian: “In fact nobody had experience with the designing and building of a VO70. What settled the matter was that Kouyoumdjian is a good team player and that he has a good grounding in technology.”
One of the challenges of designers and builders of fast sailing yachts is to get the righting moment as big as possible. The bigger the righting moment, the more performance a sailing vessel has, because the vessel is held upright as much as possible and therefore a bigger effective sail area is achieved and waterlines will be more symmetrical. One way of achieving a large righting moment is to raise the ballast percentage and lower the boat weight. All the weight you save above the waterline can be put into the keel. So, the challenge is to build hull plus its content (bulkhead, frames etc) as light as possible, but (of course) not as light that the ship falls apart. In the following the building process of the ABN AMRO boats is explained. What materials and building techniques were chosen and why?
Construction
In general, lightweight hulls are made of a sandwich construction – two stiff, strong skins with a lightweight core in between. The thicker the core is, the higher the structural stiffness. For the VO60s aramid fibres were used in the skins and foam for the core. The VO70s are made from even lighter and stiffer materials. The skins are made from carbon fibres and epoxy resin and the core is Nomex honeycomb. By using these materials the total hull structure becomes not only lighter but also stiffer. This means the rig can be strained tighter (because of less deformation of the hull), resulting in more performance.
Boats | Designer | Builder |
ABN AMRO boten | Juan Kouyoumdjian | Killian Bushe (supervisor): |
Leen Schaap | ||
Ericsson | Bruce Farr | Green Marine |
Pirates of the Carribean | Bruce Farr | Green Marine |
Movistar | Bruce Farr | Boat Speed |
Brasil 1 | Bruce Farr | ML Boatworks: Marco Landi, Indaiatuba, Brazilie |
Brunel | Don Jones | Hart Marine |
The carbon laminate is made by piling up thin layers of prepreg. Stacking these layers and the Nomex goes relatively easy (compared with aramid and foam) and is realised in about five days. After the positioning of all the layers of prepreg (11-14 layers, depending of the place in the hull) and the Nomex, the hull is packed in foil and vacuum is applied. It is then cured in the oven for 15 hours at 85°C.
“A positive factor in this project was the big volume of the oven,” says Schaap. “It is about four to five times bigger than the hull. The volume of the oven will give a very smooth setting in heat. In boatbuilding you often see the oven built around the hull. They pile up a couple of plates and pack up the boat quite narrow. Then the space is heated up. This way you do not get a favourable temperature setting. You can get hot spots: places which are very hot and right next to it cold spots. This kind of temperature difference can cause mutual shift between layers through which pre-release occurs.”
It is extremely important that the carbon skins adhere perfectly to the Nomex after curing. If the adhesion between the three layers is poor there is a risk that one of the skins releases off the core when in a rough sea or at peak stresses (delamination). Brasil 1 encountered this problem during the second leg when her deck partially delaminated. The crews of Pirates of the Carribean and Movistar also experienced it when water came into the hull through tears close to the keelbox.
VO70 (2005-2006) | VO60 (2001-2002) | |
Length (m) | 21.5 | 19.5 |
Beam (m) | 4.7-5.7 | 5.25 |
Draft (m) | 4.5 | 3.75 |
Mainsail (m2) | 172 | 83 |
Jib (m2) | 140 | 114 |
Spinnaker (m2) | 500 (max) | 300 |
Mast height (m) | 31.5 (above water) | 29 |
Displacement (kg) | 12000-14000 | 14000 |
Weight bulb (kg) | 4500 | 3000 |
Water ballast (l) | 1000 at stern | 2500 per side |
Another comparison: the weight of an Americas Cup vessel is 24 000 kg but it has only 6% more sail area than a VO70.
It is quite difficult to get good adhesion between the Nomex and carbon laminate. During the curing process the skins and core can move away from each other. Although the hull is completely packed in foil and vacuum bagged, there is still some air present in the honeycomb cells. During the cure process this air expands and in this way the air can push the carbon layers away (like a balloon) and thus destroy the adhesion with the Nomex. This can be avoided by pricking small holes in the carbon layers with a roller so that the air can escape out of the cells via the prepreg. Bushe is convinced that the adhesion between the three layers in the ABN AMRO boats is perfect.
“The prepreg package we used is from the Advanced Composites Group (England),” explains Bushe. “It included an adhesive film which is these days the standard method used for bonding honeycomb to carbon skins. Maximum pressure under the vacuum bag is very important to achieve good adhesion using these adhesive films. We have been doing this for nearly 20 years now and have the system worked out.”
In addition to bad adhesion, air voids in the carbon laminate can have disastrous results for the strength as well. Because the skin is made by placing layer on layer, air voids can get quite easily trapped between the layers. Thus the structural strength and stiffness can decrease drastically. When the first carbon fibre masts were built a lot of them went overboard because of the presence of air voids. But nowadays this kind of damage is rare. Brasil 1 did break her mast, but air voids were not the reason.
With the ABN AMRO vessels everything is done to prevent the inclusion of air voids. After installation of every layer, the hull was packed in vacuum foil. The foil was sealed airtight and the vacuum was applied. In this way any air voids present were removed.
ONE and TWO
Just for clarity, the first boat which was built is now called the ABN AMRO TWO and the second is called the ONE. The differences between the ONE and TWO are mainly in deck layout and weight. TWO was built when it was not yet clear which crew would be on which. During the building of ONE skipper Mike Sanderson and his crew were closely involved. Thus they had a lot of influence on how the deck was made, and it is an absolute advantage if you can choose how to order your tools.
Then the weight. The hull plus its content (like bulkheads and frames) of ONE is 250 kg lighter than TWO (which weights 2800 kg). First this is because the experiences which were gained by the building of TWO could be used in a positive way for ONE. Second, ONE is built in a concave (female) mould and TWO on a (male) convex mould. Schaap explains the advantages and disadvantages of these building techniques.
“The production of a convex mould is relatively simple and cheap,” he says. “A disadvantage is that the outside skin of the boat is not very smooth. Therefore the surface of TWO had to be daubed with filler that weighs about 100 kg. The building of the concave mould for ONE took about 4000 man hours of time extra. But the outside skin of the hull is very smooth, because it took on the smooth surface of the mould. Thus filling was not necessary, which resulted in a weight saving of 100 kg.”
From the design and boatbuilding point of view it appears that the success of the ABN AMRO boats is not coincidence.
“Seventy percent of our profit was gained in the preparation,” claims Heiner.
Heiner's nose for the best people and tools also played a role in the success.
“We have a strong team,” he says. “Not only the best designers and builders. Also the sailors, shore crew and staff are good.”
Their ambition was perfection. And with the motto ‘every little bit helps’ they succeeded. Mission fulfilled.
During the Volvo Ocean Race a lot of problems occurred with the canting keel systems. Here we explain the function of a canting keel and the cause of the problems. FunctionA canting keel is an alternative for water ballast. VO60s had a fixed keel with water ballast. Both systems (canting keel or water ballast) have the purpose to increase the righting moment of the boat. The advantage of a canting keel (above water ballast) is that use is made of present weight. The water for the water ballast system has to be pumped in the boat and thus makes the boat heavier and slower. A disadvantage of a canted keel is that the boat drifts more to leeward. To solve this problem the boats may apply one or two daggerboards. Most VO70s are applied with two flexible (liftable) daggerboards, one at port and one at starboard side. At broad reach courses (which often occur on this round the world race) the daggerboards can be lifted and thus decrease the wet area. This has a positive influence on boatspeed. Only Don Jones, the designer of Brunel, chose a single fixed board (canard), which is placed directly in front of the keel. But he regrets it. After the second leg Brunel goes out of the water for three legs. Changes are made at the daggerboard construction, the mast and keel. ProblemsOnly the ABN AMRO boats and Brasil 1 did not have canting keel damage during the race. In general, problems were attributed to two causes. Either the boat broke a rod of one of the hydraulic cylinders (which can cant the keel), or the boat lost one of her sliding plates. CylindersThe cylinders have a working load of 210 tons each and can cant the keel to a maximum of 40°. Since the bulb of the keel weights about 5 tons and is located 4.5 m under the vessel, the construction has to endure a lot of forces. Statically these loads are quite predictable, but dynamically it is almost impossible to predict what happens. Therefore the system has to be very strong. Both the ABN AMRO boats and Brasil 1 use a system from Cariboni. Movistar, Pirates and Ericsson use a system from Marine & Hydraulics. Both systems had problems. ABN AMRO TWO had an advantage by being in the water and sailing earlier and was able to identify and fix the problems before the race. The others were having to do it during the race. Sliding plateThe hinge of the canting keel is 150 mm inside the boat. Thus the keel can cant far to windward and can give a big righting moment. But a big hole in the hull is the result. Kouyoumdjian solved this problem with a relatively simple but ingenious design. Bruce Farr invented a system with sliding plates. But these moving plates were not resistant to the forces of the sea. Pirates lost one of her sliding plates and water came into the keelbox. The pressure was so high that the boat partially delaminated and water went seeping trough tears inside the hull. Movistar had the same problems during (the most dangerous) fourth leg through the Southern Ice sea. Water poured into the hull. Skipper Bouwe Bekking thought he had solved the keel problems by putting back the old, canting system which is made of steel. This one is heavier whereby time could be lost in the race. But with this decision Bekking hoped to stay in the race (because the old system had proved itself during training). But nevertheless Bekking said: “If we had rats onboard they would have jumped off by now.” ConclusionsAfter all, it seems that the design of Kouyoumdjian is more robust than Farr's system. Furthermore it seems that the hydraulic system of Cariboni is better for the job than the one of Marine & Hydraulics. |