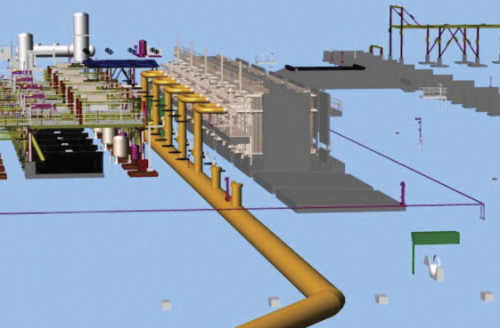







Although 2006-2010 is expected to see a downturn in the US housing market, non-residential construction – in the commercial, mining, petroleum, communications, manufacturing and chemicals sectors – is on the up, and the composites industry needs to prepare for this trend.
This was the message from Matt Lieser, global market intelligence leader for Owens Corning's Composite Solutions Business, as he opened the conference with an overview of factors driving the growth of composites in the construction and corrosion markets of North America.
The construction sector is already an important market for composites in North America, currently accounting for 24% of glass reinforced plastics' useage according to Owens Corning's figures, and Lieser outlined some of the areas where further growth is expected.
One of these is the energy market, where increasing demand for power worldwide is leading to growth in the coal, wind energy, liquid natural gas (LNG) and ethanol sectors, leading to good opportunities for composites. Production of mining and oilfield equipment has been growing strongly over the past few years, Lieser explained, and the outlook is positive for composites used in piping and other equipment. Growing demand, combined with high prices, will continue to drive exploration and production enhancement programmes in the crude oil and gas markets.
Growth is also expected in coal production through 2010, with big opportunities for fibre reinforced plastics (FRP) in stack liners, scrubbers, storage tanks and other corrosion applications in coal-fired electricity plants. LNG imports to the USA are rising rapidly and another five LNG terminals could be finished by 2008. The terminals are built near saltwater and this, combined with the chemical processing in the plant, creates opportunities for corrosion-resistant composites.
US production of ethanol, for use in fuelling cars, is increasing, and composites are used throughout the entire process, from the tractors that gather the corn, through to the tanks and pipes in the ethanol stations.
The global LNG market is being driven by increasing demand and declining domestic natural gas resources in gas-consuming countries and by the desire of gas-producing countries to commercialise their resources. The Altamira petrochemical-power complex located near the city of Tampico on the east coast of Mexico includes two new power plants and Mexico's first LNG terminal. FRP was chosen for the piping used to tranport the sea water which is used for cooling the power plants and heating the LNG for vaporisation. The picture shows the open rack vaporiser (ORV) building at the LNG plant with (in yellow) the 72 inch diameter FRP underground line connected to 26 inch diameter FRP risers. The pipes were manufactured by Plasticos Industriales de Tampico SA (PITSA).
The biggest
Several conference presentations illustrated the scale of some of the FRP projects now being carried out around the globe.
A small island in the South Pacific is the location for one of the world's largest projects for corrosion resistant FRP materials. The Goro Nickel Project taking place on New Caledonia, an overseas territory of France located between Australia and Fiji, involves the construction of a new mine, process plant and associated infrastructure. The mine is expected to produce around 60 000 tonnes of nickel and 4300-5000 tonnes of cobalt a year. Canadian-based mining group Inco is the project's main stakeholder and production at the mine is expected to begin in late 2007.
Solvent extraction technology will be used to recover the nickel and cobalt, and Dennis Southam, of Dennis Southam & Associates Pty Ltd, Australia, explained that FRP has been selected for process vessels, piping, tanks, scrubbers and stacks for many parts of the process because of the severe corrosive conditions present.
The biggest problem facing the project was the huge volume of FRP materials required. Estimated resin usage for the whole project exceeded 1500 tonnes, says Southam, and the project requirements included:
- 52 vessels and tanks, including six 14 m diameter tanks, seven 8.5 m diameter tanks, one 10 m diameter tank, and 11 high pressure multi-media filters, 0.8 m, 1.6 m and 4.0 m diameter;
- 30 km of piping, in sizes ranging from 50 NB (nominal bore) to 1200 NB, with an average size of 200 NB;
- 24 000 butt and strap joints;
- 21 pulsed columns; and
- two mixer-settlers, each 2.8 m diameter mixers and 16 m long by 8 m wide by 1.5 m deep settlers with enclosed roofs.
In the specification stage the project presented a number of challenges, according to Southam. As well as being able to withstand severe corrosive conditions some applications also required fire retardance and electrical conductivity. Fire retardance was achieved using suitable fire retardant resins and electrical conductivity by using carbon filler and carbon surface veil.
To supply all this equipment, orders went to fabricators in Israel, China, India, Australia, Indonesia, Singapore and the Philippines. Given the fact that FRP equipment would be manufactured in many countries the specification allowed for design and manufacture to recognised codes such as BS 4994, EN 13121, ASME RTP-1 and ASME Section X.
A key concept for the project was modularisation. This is to minimise site work as far as possible, given the difficult conditions, including hot and humid weather. Much of the equipment collected from around the world ended up initially in the Philippines, where yards were established to put together the various modules for final shipment to site. The largest of the modules weighed around 500 tonnes.
The single largest use of FRP was in the pulse columns. In the patented Bateman pulsed column technology for solvent extraction the solvent and aqueous phases are separated in a vertical column using pulses of air. The column consists of a large diameter vertical pipe filled alternately with disc and annular shaped (‘doughnut’) baffles which facilitate contact between the immiscible liquids passing through the column. The columns are pulsed by blowing air at the required amplitude and frequency into the pulse leg.
The pulsed columns for the Goro Nickel Project are the largest ever designed, with an active section of 4 m diameter and height up to 40 m. There are two solvent extraction plants for nickel and cobalt, comprising a total of 21 pulsed columns. Each of 19 of these 21 pulsed columns has a bottom decanter (5.5 m diameter for this project), the 4 m diameter active section, and an upper decanter, also 5.5 m diameter. The size of these columns presented design challenges, particularly in terms of the wind and seismic loadings.
The tonnage of laminate for the pulsed columns was so large (total resin usage approximately 720 tonnes) that manufacture for the various components had to be spread between four companies. Bottom decanters and active sections were manufactured in Israel, top decanters and discs and doughnuts were manufactured in Indonesia, and pulsation legs (1.6 m diameter) and spacer rods for the discs and doughnuts were fabricated in India.
Another major package was the six 14 m diameter, 8 m high and 18 m high storage tanks (plus other tanks ranging from 10 m diameter down to 1 m diameter), which were manufactured in China. Normally FRP tanks of this size would be wound on site but in this case they had to be manufactured off site and transported. It is believed that these would be the largest FRP tanks transported as a complete vessel. A vertical winder was designed and built specifically for this exercise. The tanks had to be shipped by barge up the Pearl River to the nearest international shipping port of Hong Kong, via the port at Zhongshan, and loaded by crane on to a ship for transport to site.
Most of the general equipment items have now been manufactured, says Southam, including the pulsed columns and pressure filters. Pipe manufacture is almost complete, and the first of the 14 m diameter tanks is in the process of being shipped.
Another impressive corrosion project discussed at the conference was the construction of two GRP storage tanks by Indonesian company Pt. Gunung Putri Grama Mas. With a diameter of 20 m and shell height of 15.8 m, these are believed to be the largest FRP chemical storage tanks manufactured to date. The tanks are each designed to hold 5000 m3 of phosphoric acid and are installed at a fertiliser plant in West Sumatra Island, Indonesia. The job was performed on site and because of the remote location, it took nearly one year to complete. An epoxy vinyl ester resin supplied by Swancor was used for the corrosion barrier, and an isophthalic resin was used for the structure. The dished top cover was fabricated in 16 segments with a crown radius of 20 m.
FGD
Flue gas desulphurisation (FGD) equipment started to be deployed on coal-fired power stations around the world in the 1970s-1980s to reduce emissions of sulphur dioxide (SO2) to the atmosphere. There are various technologies available. The most common are wet FGD processes in which an alkali (often a slurry) is contacted with the flue gas in a spray tower to form a week acid solution that reacts with and is neutralised by the dissolved alkali. The sulphite and sulphate products produced precipitate out of solution and can be recovered. In dry systems the alkali sorbent is either injected into the gas stream or the gas is passed through a bed of the sorbent. The corrosive conditions encountered in these processes lead to applications for FRP in components such as spray tower absorption scrubbers, chimney/stack liners, pipes, ducting and tanks.
The market for FGD equipment – for retrofit on existing plants and on new plants – continues to grow around the world and according to a McIlvaine Company report, power plants will spend around US$168 billion on FGD systems during the period 2005-2020. In the USA the Environmental Protection Agency (EPA)'s Clean Air Interstate Rule requires states to reduce SO2emissions from 2003 levels by the order of 57% by 2015.
Rick Solar, FGD Program Manager, and Eric Sprinkle, AQCS Project Manager, for engineering, consulting and construction group Black and Veatch Engineering Co agree with this positive forecast. For Black & Veatch the market was strong during 2004-2006, and although it is seeing a decrease in activity in 2007-2008 the company says the next round of projects will begin in 2009 to support US 2015 emissions reduction regulations. It estimates that only 35% of the retrofit FGD projects which will be required in the USA have been contracted to date.
Although all this is good news for composites, Solar and Sprinkle also outlined some significant areas of concern, including the following:
- the capacity of FRP fabricators might not be adequate to support the market;
- design issues – - many projects a first for fabricators;
- ability of fabricators to meet delivery schedules;
- demand of a single project can consume a majority of the shop capacity; and
- reluctance of some fabricators to expand to meet market demands.
Black & Veatch has the North America license for Japanese company Chiyoda Corp's FGD technology CT-121™, which relies on the extensive use of FRP. Rather than spraying limestone slurry into the flue gas as in a conventional spray tower, in the Chiyoda technology flue gas is first quenched by cooling sprays and then enters a jet bubbling reactor (JBR) where it flows down through vertical gas sparger tubes to the absorption slurry. Cleaned flue gas passes upwards through gas risers into the upper plenum and on to the mist eliminator system.
A typical FRP shell for a 600 MW JBR is 88 ft in diameter with a straight side height of 72 ft, slurry capacity of 1 200 000 gallons and an empty weight of 700 000 lbs. The laminate design would consist of a corrosion barrier (a vinyl ester resin with abrasion-resistant liner in the slurry area, reinforced with one layer of glass at the inner surface and multiple layers of chopped strand), a structural wall using a vinyl ester resin reinforced with filament winding at around 90°, and an exterior shell of vinyl ester resin reinforced with soft chopped strand and glass layers at the outer surface. This would be topped with a UV surface coat in opaque white.
FRP is also used in the internal components of the JBR, including support structure, deck panels, gas risers, deck wash systems, and the oxidation air distribution system. Standard FRP components are used, such as abrasion-resistant pultruded structural components and deck panels. Stack liners are field wound either exterior or interior to the stack; these are approximately 30 ft in diameter, with a height up to 1000 ft. Fire retardant vinyl ester resin is used in their construction and they are installed from bottom to top by jacking flue can sections. FRP is also used in the FGD system outlet ductwork and piping.
New technologies
As worldwide demand for energy continues to grow and countries attempt to decrease their dependency on petroleum resources, attention has increasingly turned to ‘clean’ coal technologies. One of these is coal gasification and John F. Kamody, corrosion consultant for Reichhold Inc, sees good opportunities for composites in this process. Coal gasification has already been commercially proven on a large scale throughout the world. Lately the process has been receiving increasing attention for dependable and affordable supply of hydrogen and other clean fuels.
One person in everyone's thoughts at this year's conference, the 15th in the series, was Dr Frank Cassis, the ‘founding father of the corrosion industry,’ who died earlier this year. The Construction, Corrosion and Infrastructure conferences were initiated by Cassis and many of the speakers and exhibitors at this year's event spoke of his passion for the industry, and of how he ‘persuaded’ them to contribute. Cassis, whose composites career spanned 50 years, was best known in the industry for establishing isophthalic polyester resins in the corrosion-resistant equipment sector and particularly in underground gasoline storage tanks. During this year's event the 2007 Dr Frank A. Cassis Award for Exceptional Achievement in the Corrosion and Composites Industry was presented to Dr Joseph M. Plecnik, a consultant, designer and educator with over 30 years of service to the FRP composites industry, specialising in free-standing composite smoke stacks. Plecnik is currently a professor at the Structural Composites Laboratory at California State University in Long Beach. The Construction, Corrosion and Infrastructure conference is held every two years by the Western Chapter of the American Composites Manufacturers Assocation (ACMA). |
Coal gasification involves the incomplete combustion of coal in order to produce a gas rich in carbon monoxide (CO) and hydrogen (H2); the sulphur contained in the coal is converted predominantly to hydrogen sulphide (H2S). After entrained particulates are removed by scrubbing, the gas is simultaneously cooled by saturation with water. The acid gases (H2S and CO2) are selectively removed and the resulting CO and H2 can be used as an industrial fuel or upgraded to yield clean synthetic fuels and chemical products such as methanol, ammonia or hydrogen. Recovered H2S is converted to elemental sulphur and CO2 may be sequestered or used externally in enhanced oil recovery.
The most widespread commercialisation of coal gasification has occurred outside the USA, particularly in countries which lack petroleum and natural gas resources or the associated infrastructure. Major US projects include the coal-based production of acetic anhydride by Eastman Chemical Co in Kingsport, Tennessee, and a coal-based methane plant in Buleah, North Dakota. Although there are basic differences between coal combustion and gasification, there are similarities when it comes to corrosion and the associated benefits afforded by composites, says Kamody.
Infrastructure challenges
The third focus of the conference was the application of composites in infrastucture, in areas such as bridge decks, blast protection, and repair and strengthening techniques.
The US construction industry is very slow to accept innovations – it is not unheard of for an innovative idea to take 10-25 years to penetrate and become accepted by the construction industry, explained Muhammad Amer, senior program manager, American Society of Civil Engineers (ASCE) and Marvin Oey, director of the ASCE's Construction Institute. This is one of the barriers facing composites in the infrastructure market. Others include a significant lack of investment in existing innovative technologies, a highly fragmented market (around 50 000 building codes, more than 100 000 design firms, and over 1 million contractors), and reluctance of contractors to adopt new technologies because of the financial risks and regulatory hurdles.
A highly competitive business environment and continuous pressure to reduce costs are further challenges facing FRP materials, but there are examples of success stories. Rob Banerjee, vice president, business development, WebCore Technologies Inc described the potential applications of the company's TYCOR core material developed for sandwich structures in construction, infrastructure and industrial applications, and particularly for highly corrosive environments. Tycor is based on a patented fibre reinforcing technology that places glass fibre reinforcements through the thickness of closed cell foam sheets to produce a web and truss structure. The cores are said to be ideally suited to vacuum infusion and other closed moulding processes.
In infrastructure applications Tycor sandwich panels can be used to create decks for pedestrian and vehicular bridges. Other potential applications under development include lightweight, modular military bridges, and road mats for use by heavy-duty vehicles on soft soil, mud or ice. In corrosion applications, Tycor sandwich panels could be used to replace thick laminates currently used in inlet/outlet ducts, scrubber roof panels, interior decks and beams, chimney liner divider walls, chimney floors and breaches, offering quicker production time for large parts, easier handling and faster installation.
International Paper installed five pulp mill roofs using Tycor sandwich panels in 1996, replacing reinforced concrete roof. The composite panels have now over 10 years of service history in this highly corrosive environment without any problem; the typical life of a concrete roof was 10 years.